So you have a lot of valuable assets that you’re having trouble keeping track of. Maybe it’s the IT items in your data center that are constantly on the move. Perhaps it’s expensive lab equipment or tools that always seems to go missing. It could be returnable containers that don’t get returned or important files that never are where they’re supposed to be. You’re pretty sure RFID can help you manage the situation better, but you need to do some sort of Return on Investment to justify the purchase. How do you start this? What parameters should you consider? What method should you use? Let’s look at these.
QUANTIFYING THE CURRENT SITUATION
The single most important aspect of any ROI calculation (and perhaps the one most challenging to ascertain) is determining the costs of the existing process. It’s one thing to know that items are lost, it’s another thing to know how many are lost, and yet another to assign a proper value to them. But having this information is imperative as it becomes the baseline against which all future improvements are measured.
So how is this gathered? The answer is that it will depend on the unique nature of your operation. Every company uses different processes and has different issues impacting it, the key is to discern what the most important of these issues are and come up with a way to define their economic impact. The best way to do that is to ask a series of questions that helps ferret out the information. Some examples are:
- What are the items that matter and require better accountability? This should be as specific as possible. If, for example, the answer is “tools,” is it all tools or only tools of a certain value? Is it only tools that need to be calibrated? Is it only tools used by a particular department or assigned to a certain project? Is it all of the above?
- What is the current visibility as to location accuracy for these items. Quantify, as best as possible, the inventory accuracy. If a recent audit has been performed, that’s a good start. But other ways to address this are to ask, “How many times per day/week/month can something not be located out of all of the times that it is needed?” or “How frequently are items in short supply and typically by how much?”
- What is the intrinsic value of these items? The actual cost of a data tape may be $50. But the cost of losing its sensitive information could be millions. When assigning monetary figures to anything, ask “What would the cost impact be of losing this item?” In some cases (i.e., a work of art), the item may be priceless.
- What are the current costs for managing these items? How are accountability issues handled today? If something is missing, how is it located? What is the cost impact of this (1 person spends 10 hours per week searching for items at a cost of $X per hour)? Do replacements need to be ordered at expedited freight charges? What is that cost? Do physical audits need to be taken routinely to maintain accountability? Factor in the overall costs of these?
- What are the ancillary costs associated with the missing items? In addition to the direct costs of managing the items, what are the other costs associated with losing them? What is the lost revenue associated with not having finished product available? What are the impacts to manufacturing when raw materials or tooling are not available? How does lack of visibility impact financial accountability for depreciation and Sarbanes-Oxley reporting? How does inventory inaccuracy impact other departments? Customers?
There may be other cost factors associated with your particular situation. Be careful to consider them all. One of the challenges in calculating a return on any technology such as RFID is that the costs are often hard to describe monetarily. They may include items such as reduced customer satisfaction or diminished productivity, which certainly are of value, but are hard to relate to dollars. Still, these need to be calculated as best as possible to complete a full ROI analysis of the project.
Once these answers are established, you can develop a basic understanding of the existing visibility situation. On the most basic level, a calculation can be as follows:
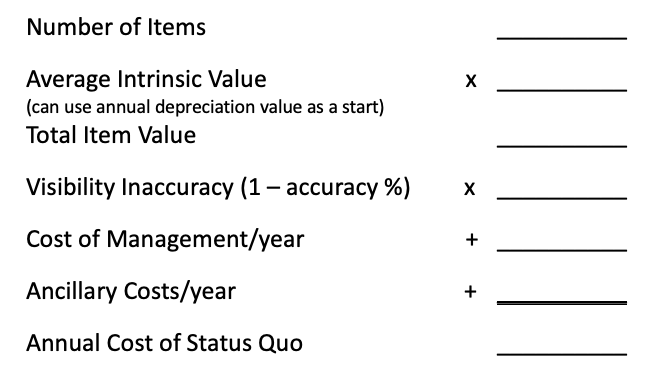
This figure represents the problem’s total cost and the potential cost savings if the problem is 100% solved. With knowledge of this basic formula, let’s look at an example.
Example: A manufacturer often spends hours searching for high value tools and equipment that need to be calibrated on a regular basis.
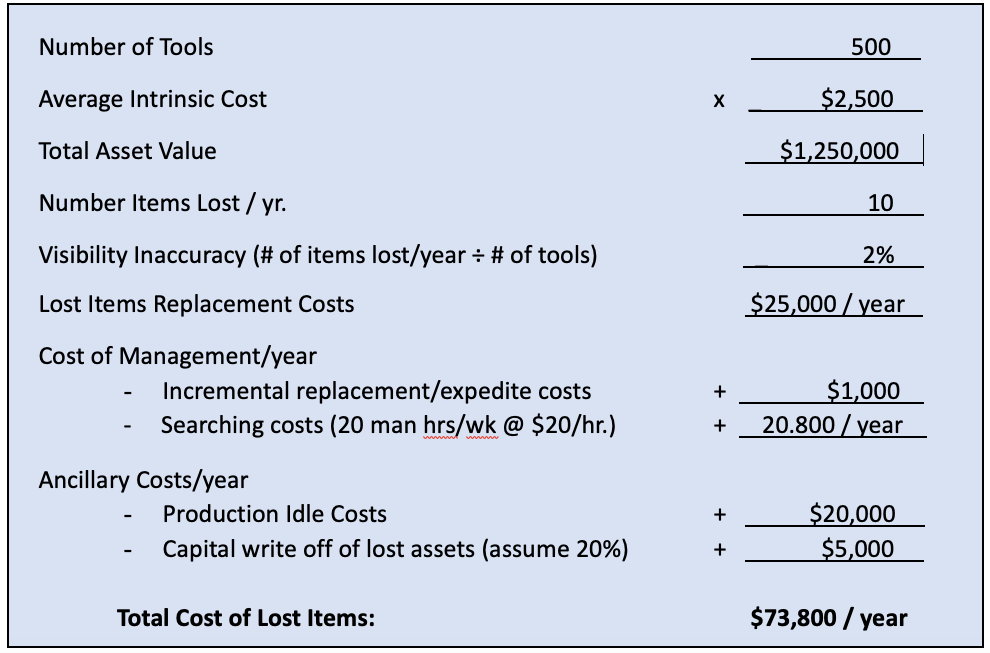
DETERMINING THE PROPER ROI CALCULATION
Armed with the knowledge of your existing cost structure, the next question is to determine the proper ROI calculation to use. There are over a dozen accounting formulas that are used to quantify a certain return on an investment, and each has a unique value in its perspective. Most experts, though, consider Net Present Value (NPV) to be the best formula to use.
NPV is defined as “the difference between the present value of cash inflows and the present value of cash outflows. NPV is used in capital budgeting to analyze the profitability of an investment or project.” The formula is:
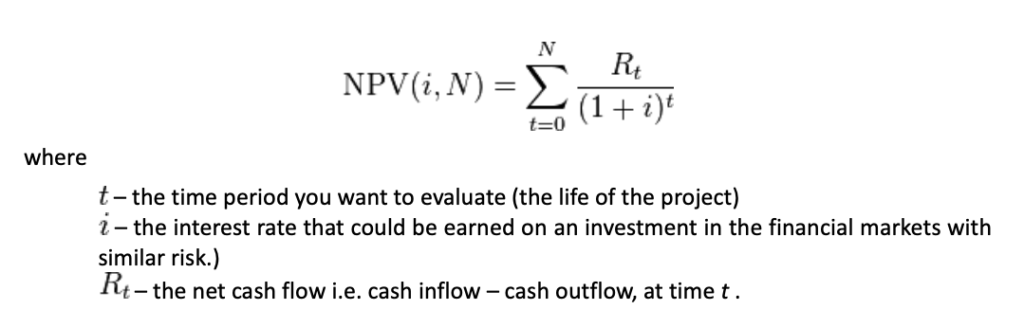
In short, it’s a calculation where you determine if the projected financial benefits outweigh the projected costs. A positive result is favorable; a negative one is not. Determining the projected cost is rather simple. Costs include the depreciated costs of the hardware plus reoccurring costs such as tags, software, etc. The projected benefits equal the cost savings we listed above.
If we use the asset tracking scenario in our example as a case study, we will make the following assumptions:
- The cost of the required hardware and services is $100,000 and fully depreciated evenly over five years ($20,000/year).
- The reoccurring annual software license is $30,000 per year. Reoccurring tag costs equal $5,000 per year.
- The market interest rate is projected to average 7% over the 5-year project life.
Then the calculation would be:
(The annual cost savings) – (The yearly system costs) x five years divided by the interest rate, or as follows:

Thus, this project would have a positive benefit to the company, saving them $67,143 over five years.
Use this as a start for your calculations.